Oil and gas inspection is vital in production facilities to ensure safety. The stakes are high– missing even minor details can result in equipment failure, accidents, expensive production halts, or even environmental disasters.
Traditional inspection methods come with inherent challenges. They are error-prone, time-intensive, relying heavily on manual data collection, extensive paperwork, and disjointed systems. However, a digital inspection app can revolutionize your inspection process.
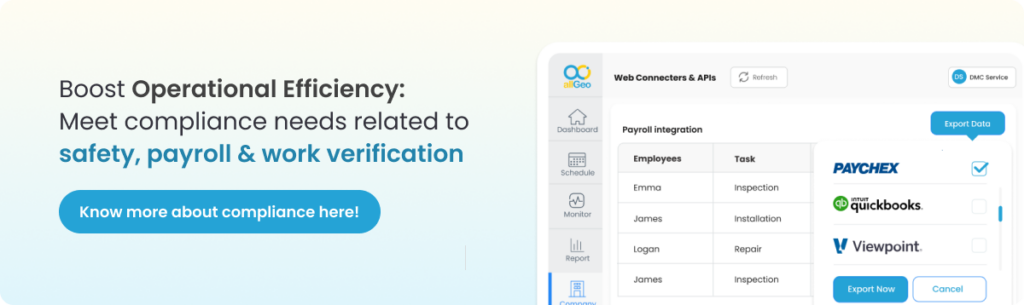
Inspectors in the oil and gas industry often operate in remote locations. They collect detailed data and document their findings to comply with regulatory standards. After conducting physical and visual inspections, they typically compile handwritten notes and photographs into spreadsheets. This is followed by the time-consuming task of manually preparing deficiency reports, which are often managed through a combination of emails and spreadsheets.
Incorporating digital solutions into inspection and maintenance practices is essential for modern oilfield operations.
Automating periodic inspections’ data collection processes in oilfields reduces downtime significantly. By digitizing inspection data collection and integrating it into centralized databases, companies can streamline reporting and enhance decision-making.
Technology offers a transformative way to manage oil and gas inspections. Let’s identify the gaps in your inspection process that could be draining valuable productive hours.
Spreadsheets
While spreadsheets have been a common tool in oil and gas inspections, they often create bottlenecks and inefficiencies in the process. Here’s how:
Time-consuming data entry: Manually entering data into spreadsheets is a tedious process, especially with the large volumes of information gathered during inspections. This takes inspectors away from their primary task of assessing equipment and identifying potential issues.
Increased risk of errors: Manual data entry is prone to human error, such as typos and incorrect data entry. These errors can compromise the accuracy and reliability of inspection reports.
Cumbersome reporting: Generating reports from spreadsheets can be a manual and time-consuming process. Extracting and formatting data for reports can delay communication and slow down decision-making.
Solution: Inspection Mobile App
Replacing spreadsheets with a field inspection mobile app offers an efficient solution-
Streamlined data capture: Mobile apps allow inspectors to record data directly on their smartphones or tablets. Apps like allGeo support all forms of data such as notes, pictures etc.
Real-time collaboration: Mobile apps facilitate real-time data sharing and collaboration among team members. Everyone can access the most up-to-date information, eliminating version control issues and promoting seamless communication.
Advanced analytics and reporting: Many mobile apps such as allGeo empower oil and gas inspections with robust data analytics and BI reporting. You can monitor key performance indicators (KPIs) like inspection completion rates and progress towards operational goals. Further, you can leverage data-driven insights for maintenance schedules and resource allocation.
By transitioning from spreadsheets to a mobile app solution, oil and gas companies can significantly improve the efficiency, accuracy, and overall effectiveness of their inspection processes.
Paper-based inspection process
Paper checklists in the oil and gas inspections introduce several inefficiencies. It can significantly slow down inspections and hinder overall operations.
Take the case of non-conformance i.e. when equipment fails to meet established standards. Resolving it typically involves a manual process: detailed deficiency reports, emails to responsible parties, and tracking progress in spreadsheets.
For instance, if an inspector identifies a critical non-conformance on-site, they will manually document the issue. It typically involves taking photographs, and later compiling this information into a written report. The challenges it poses are-
Time-Intensive and Error-Prone Documentation: Paper data entry slows down inspections, especially in complex scenarios requiring detailed notes and multiple forms. Handwritten records are prone to errors, misinterpretation, omissions and even misplacement.
Limited Accessibility and Collaboration: Paper records are often stored in a single location. It can be difficult for stakeholders to access or share data in real time. This hinders collaboration, delays approvals, and slows down decision-making processes.
Inefficient Tracking and Follow-Up: Without a centralized system, tracking inspection statuses, resolving deficiencies, and maintaining schedules become cumbersome. Missed follow-ups can result in costly downtime or safety risks.
Solution: Digital checklists and Mobile Forms
You can perform oil & gas inspections, audits, and more with a digital inspection checklist that can be accessed and filled out from any device. Digital checklists offer a simple, efficient way to standardize inspection processes. Easily create and customize online inspection forms with allGeo’s drag & drop form builder. Here is how it can save you time in your inspection process-
Streamline Service Inspections with Digital Checklists: Switching from paper-based inspection processes to digital checklists can significantly enhance efficiency in the oil and gas sector. Tailored digital forms can be customized to meet specific inspection needs and adhere to industry standards.
Real-Time Dispatch and Dynamic Scheduling: Mobile inspection forms simplify job-site operations by enabling real-time dispatching. Whether it’s a planned inspection or an urgent change in schedule, digital checklists allow managers to quickly send the right forms to the right technician at the right location.
Offline Access and Accurate Geo-Tagging: Oil and gas inspections often occur in remote areas with limited connectivity. allGeo’s digital inspection forms overcome this challenge by allowing offline access, so technicians can complete their tasks without interruption. Moreover, these forms are geo-tagged, providing precise time and location data for every inspection.
The inspector completes their rounds, logs observations directly into the digital inspection platform, and generates a comprehensive report with a single tap. The report is instantly synced to the cloud, ensuring immediate access and seamless sharing.
Conclusion
Managing oil and gas facilities is a complex undertaking, requiring meticulous coordination and constant vigilance. By automating inspections, companies can maintain safer, more efficient operations while staying ahead of regulatory requirements. Automation isn’t just a convenience—it’s a necessity in driving operational excellence and safeguarding both people and assets.
Field managers, engineering geologists, pipeline technicians, and other professionals face a multitude of challenges during inspections. Automating key aspects of inspection management can transform what once took days into tasks completed in mere minutes. From reviewing and approving inspection reports to leveraging powerful analytics for data-driven decisions, digital tools enhance both efficiency and compliance.