Businesses face quality-related risks at various stages of the production process, especially in industries like construction. Deviations in raw materials, human errors, ineffective change management, and evolving regulatory requirements all contribute to potential quality issues.
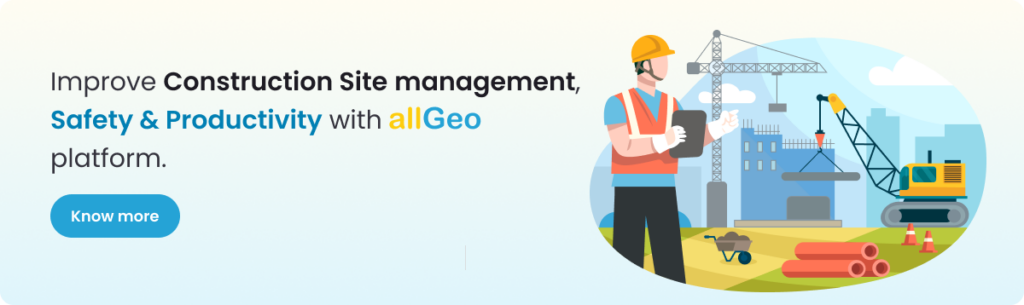
For construction site managers and quality assurance teams, routine inspections are essential for monitoring progress, managing risks, and maintaining safety standards. Regular site checks allow project managers to:
- Identify hazards, such as misplaced equipment or unsafe work conditions.
- Address inefficiencies that could cause delays or additional costs.
- Promote a safer work environment, reducing accidents and ensuring regulatory compliance.
To systematically identify and resolve quality gaps early in the project lifecycle, inspections are necessary. It helps identify minor issues from escalating into significant problems. A robust inspection process not only minimizes risks but also strengthens overall project quality and compliance.
Here are 6 effective strategies to enhance quality during a construction inspection:
1. Integrate Inspections into the Construction Quality Plan
Construction site inspections are often treated as isolated activities, rather than being embedded into the overall project framework. Incorporating inspections directly into the plan from the beginning ensures that quality is a part of the project’s foundation and execution.
Furthermore, integrating inspections into the quality plan communicates a strong commitment to quality to all stakeholders. It emphasizes that quality assurance isn’t an afterthought—it’s a continuous process woven into every stage of the project lifecycle.
2. Equip Inspection Teams with Comprehensive Training
For inspection teams to perform effectively, they must have a thorough understanding of regulatory requirements, quality standards, and the critical role inspections play in project success. Effective inspections go beyond simply assessing the site—they involve observing work processes, interviewing workers to verify standardization, documenting findings, and ensuring proper follow-up and communication.
To achieve this, training programs must be robust and tailored to equip teams with the necessary skills and knowledge. Comprehensive training empowers inspectors to carry out their responsibilities with precision, ensuring strict adherence to processes and improving overall compliance. This investment in training not only enhances the quality of inspections but also reinforces a culture of accountability.
3. Implement Reliable Inspection Checklists
Relying solely on informal site walkarounds can lead to gaps in oversight, with unclear records of what was inspected or what met quality standards. By adopting construction inspection checklists, these challenges can be avoided. Checklists provide a structured approach to inspections, ensuring nothing critical is overlooked while saving valuable time.
Construction managers should create detailed checklists that outline specific items to verify at every milestone. These should include health and safety requirements, quality control measures, and checkpoints that require photo evidence or precise measurement data. Such detailed checklists improve the accuracy and consistency of inspections.
Additionally, using these checklists as training tools ensures that all inspectors are aligned on what to look for and how to document their findings. Standardized formats and procedures promote uniformity across inspections.
4. Establish Clear Quality Standards
A well-defined quality statement is essential to guide an organization’s policies and processes. It serves as the foundation for quality management procedures, ensuring alignment among quality teams, suppliers, and other stakeholders. These documented standards act as a reference point for conducting inspections and audits, enabling teams to implement consistent quality checks throughout every phase of the project.
From raw materials to production workflows, adhering to documented quality standards ensures compliance with Standard Operating Procedures (SOPs) and minimizes deviations.
5. Develop Streamlined Inspection Workflows and Measurable Metrics
Inspection workflows should be simple, intuitive, and easy to execute, especially in medium to large-scale operations where multiple units and processes require oversight. To ensure clarity and efficiency, workflows should be broken into manageable steps, enabling implementation with minimal training. This not only enhances the overall effectiveness of inspections but also shortens the inspection time cycle.
In addition, establishing clear, measurable metrics for key parameters allows inspectors to quickly identify deviations from quality standards. By combining streamlined workflows with data-driven metrics, businesses can create a more efficient, consistent, and effective inspection process that improves overall project quality.
6. Maintain OSHA-Compliant Safety Reporting
Inadequate safety measures can significantly impact the overall quality of a construction project. Inspections present a valuable opportunity to confirm that safety protocols are properly implemented alongside quality checks. To ensure compliance, inspectors must document and report all safety hazards identified during the inspection process in line with OSHA regulations.
By integrating safety reporting into inspection workflows, construction teams can proactively address hazards, protect workers, and maintain compliance with industry safety standards, ultimately supporting both project quality and workplace safety.
Conclusion
Improving quality of construction inspections requires a structured approach. Streamlined workflows, measurable metrics, and clear documentation of quality standards further enhance the inspection process, enabling teams to identify and resolve issues efficiently.
Additionally, adhering to OSHA-compliant safety reporting ensures that safety and quality go hand in hand. When inspections are performed with precision, supported by well-defined processes and tools, construction projects can meet quality benchmarks, stay on schedule, and deliver safe, reliable results that exceed stakeholder expectations.