Running a successful manufacturing company hinges on effective workforce management, as labor is the backbone of the organization. However, many managers struggle with accurately calculating labor cost—a critical metric that directly impacts a company’s profit and loss analysis.
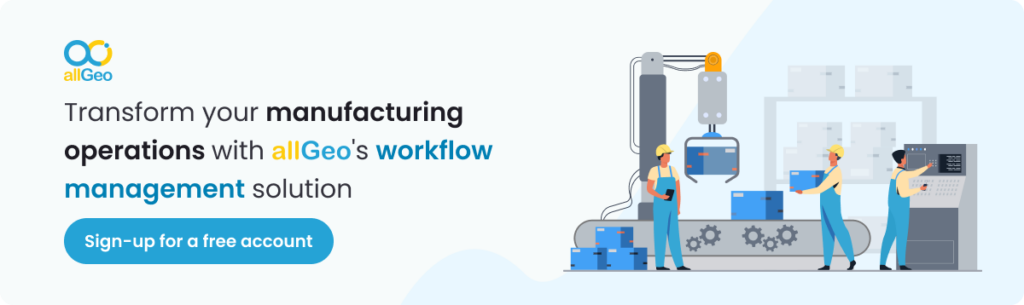
Without a clear understanding of these costs, you are leaving gaps in your financial insights and not tracking where your money is going. Mastering labor cost calculations provides clarity, enabling better control over production processes, uncovering cost-saving opportunities, and ultimately driving profitability.
Businesses in manufacturing must monitor labor cost for factory work to improve profitability and streamline workflows. Read ahead to understand how to calculate labor costs in manufacturing.
What is Labor Cost in Manufacturing?
Labor cost in manufacturing refers to the total expenditure a company incurs on its workforce. This includes more than just wages for salaried and hourly workers—it also encompasses costs for contract labor, employee taxes, bonuses, overtime, sick pay, maternity leave, and additional expenses like training and employee compensation programs.
For many companies, especially small to medium-sized businesses, labor costs represent a significant portion of overall operational expenses. Tracking these costs comprehensively is crucial to maintain profitability, as they go far beyond basic salaries. The easiest way to do so is by tracking the hours worked using an automated time tracker designed for manufacturing operations.
What’s the difference between direct and indirect costs?
Accurately calculating labor costs in manufacturing requires distinguishing between indirect and direct cost of labor. Both play a significant impact production expenses. Here’s a breakdown:
Direct Costs
Direct cost of labor are the expenses that can be traced specifically and exclusively to the production of a particular product. These costs are directly tied to the manufacturing process and include:
- Direct Materials: The raw materials or components used to create the final product. For example, in a light bulb factory, the glass and filaments are direct material costs.
- Direct Labor: Wages and benefits paid to employees directly involved in producing the product, such as assembly line workers, machine operators, and technicians. This also includes overtime pay, payroll taxes, and benefits like health insurance or retirement contributions.
- Production Utilities: Utilities such as electricity, water, and natural gas directly consumed in manufacturing the product.
Indirect Costs
Manufacturing overheads, or indirect costs, include expenses that don’t directly tie to a specific product but are essential for overall production operations. These costs include:
- Administrative Salaries: Pay for employees like office managers, payroll staff, and administrative assistants who support the business but don’t directly work on production.
- Overhead Expenses: Costs such as rent, insurance, property taxes, and equipment maintenance that support the manufacturing process.
- Quality Control: Expenses related to ensuring products meet standards, even though these are not tied to a specific unit.
- Opportunity Costs: Financial losses incurred due to inefficiencies or missed opportunities.
For example, in a factory, the salaries of supervisors who oversee production without directly working on products and costs for facility maintenance fall under indirect costs. According to McKinsey, indirect costs often account for 8-12% of total manufacturing expenses.
How To Calculate Labor Cost?
Understanding how to calculate manufacturing labor costs is crucial for managing expenses and ensuring profitability. By breaking the process into key components, you can get an accurate picture of labor costs and identify areas for optimization. Here’s how to calculate manufacturing labor costs step by step:
1. Calculate the Hourly Labor Rate
The hourly labor rate represents the total cost of employing a worker for one hour. This includes wages, payroll taxes, and benefits. To calculate it:
- Hourly Labor Rate Formula: Hourly Labor Rate= Wages + Taxes + Benefits / Total Hours Worked in the Period
This step gives you the direct hourly cost of labor for your manufacturing operation.
2. Calculate Labor Hours Per Unit
The next step determines how many hours of labor are required to produce a single unit of your product. It is an essential metric for understanding labor efficiency.
- Labor Hours Per Unit Formula: Labor Hours Per Unit= Total Units Produced / Total Hours Worked
This calculation helps you understand how much time it takes to manufacture each unit, which is a vital component in determining production costs.
3. Calculate Labor Cost Per Unit
The labor cost per unit reveals how much labor expense is attributed to each individual product. It combines the hourly labor rate and the labor hours per unit.
- Labor Cost Per Unit Formula: Labor Cost Per Unit= Hourly Labor Rate × Labor Hours Per Unit
This metric highlights how labor contributes to the overall cost of manufacturing each product and provides a foundation for evaluating pricing strategies.
Conclusion
After calculating your labor costs, you may find that labor expenses make up a significant portion of your overall production costs. This insight can guide your next steps, such as:
- Reducing labor costs through process improvements, automated time and attendance tracking, overtime calculation etc.
- Adjusting your product pricing to reflect labor expenses.
- Have a robust scheduling system in place to avoid manual errors.
Understanding and monitoring these calculations allow you to optimize costs, and maintain profitability in a competitive manufacturing environment.